By Edvard Csanyi
Energy Saving Potential
Efficiencies of fan systems vary considerably across impeller types. The average energy saving potential in these systems in the U.S. manufacturing industry is estimated at 6%. For optimal savings and performance, it is recommended that a systems approach is used.
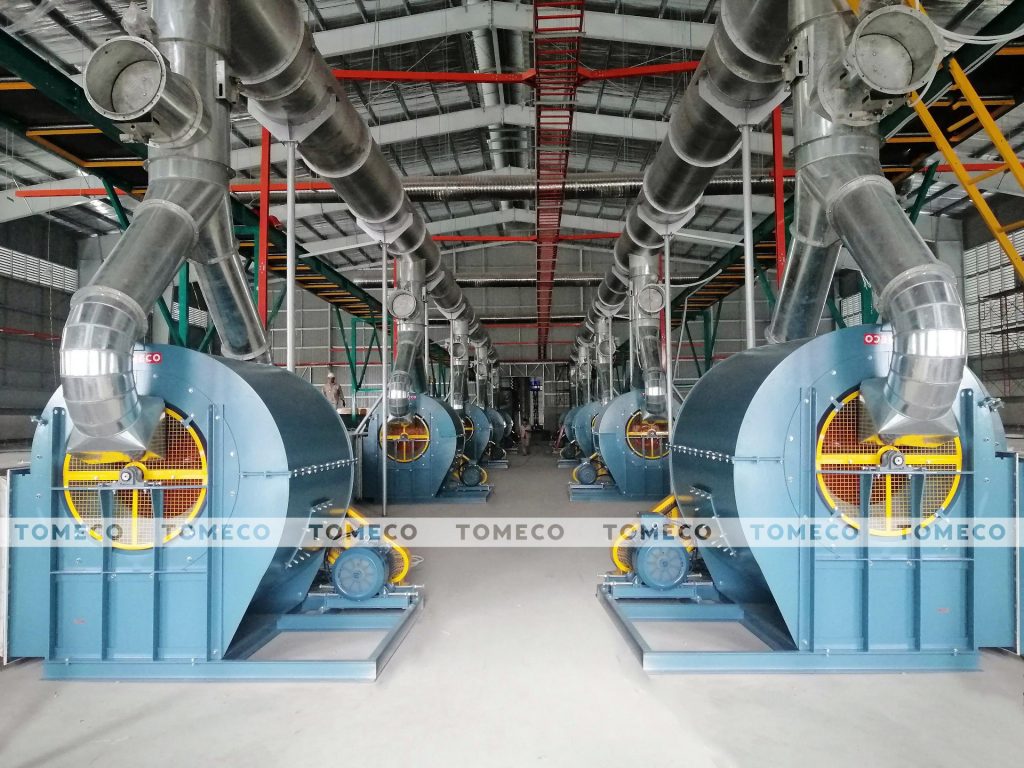
1. Minimizing pressure
Pressure offers greater opportunities to reduce energy costs. A system with good airflow characteristics (duct and sizes optimized), matched with the proper control device, pressure monitors, and variable-frequency drives, can help manage system pressure.
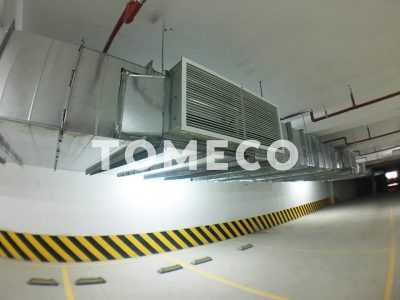
Most baghouses or other collection devices will have varying pressure drops over the life of the system. Bags are generally more efficient at higher pressure drops, but then use more energy.
![]() | A good pressure monitoring system that controls system volumetric flow rate can save thousands of dollars every year on the operation of even medium-sized systems. |
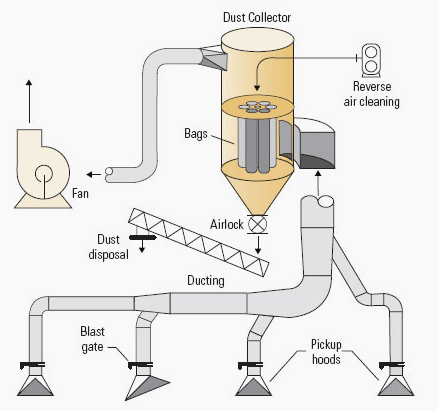
As ASDs become less expensive they are now being found on many installations. Be mindful of duct inefficiencies and fan system effects (elbows at inlets and outlets, etc.) These shortcuts increase static pressure and operating costs for the life of the system.
2. Control density
Temperature, moisture, molecular weight, elevation, and the absolute pressure in the duct or vessel affect the density of the transporting gas. A density change may affect the hardware requirements for the system.
![]() | Evaporative cooling, for example, reduces volume, but the higherdensity air requires more power. |
This may be more than offset by reduced costs for smaller ducts, control devices, and fans (as well as lower the value for volumetric flow rate in the equation).

3. Fan efficiency
The key to any design is proper fan selection. The design of the fan and its blade type can affect efficiency and power requirements significantly. Laboratory-measured peak fan efficiency may not be the most stable point of operation.
![]() | If peak efficiency coincides with the peak of the pressure curve then there may be operational problems as volumetric flow rates vary with small changes in system pressure. |
The designer must consider both curves when selecting the best fan and operating point to optimize reliability and power usage. Fan type may dictate proper selection. Airfoil wheels, while more efficient, may not be a good choice when handling particulate laden air.
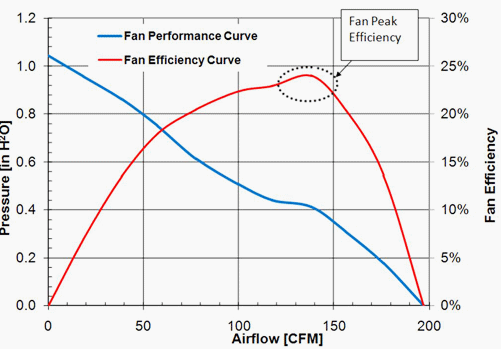
4. Proper fan sizing
Most of the fans are oversized for the particular application, which can result in efficiency losses of 1-5%. However, it may be more cost-effective to control the speed than to replace the fan system.
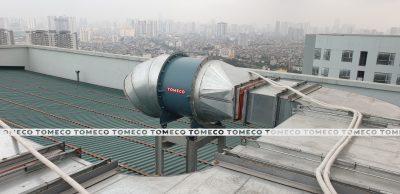
5. Adjustable speed drives (ASDs)
Significant energy savings can be achieved by installing adjustable speed drives on fans. Savings may vary between 14 and 49% of fan system energy use when retrofitting fans with ASDs.
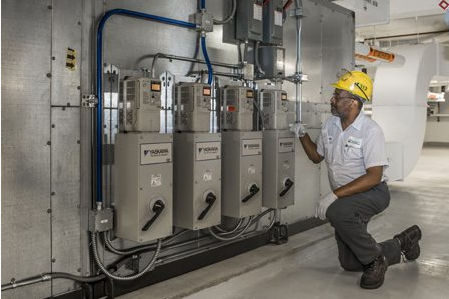
6. High efficiency belts (cogged belts)
Belts make up a variable, but significant portion of the fan system in many plants. Standard V-belts tend to stretch, slip, bend and compress, which lead to a loss of efficiency.
![]() | Replacing standard V-belts with cogged belts can save energy and money, even as a retrofit. Cogged belts run cooler, last longer, require less maintenance and have an efficiency that is about 2% higher than standard V-belts. |
Typical payback periods will vary from less than one year to three years.

Source: electrical-engineering-portal.com